
PUSHING BACK...
AGAINST PLANTER COMPACTION
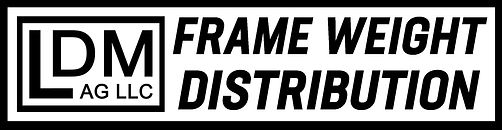
Over the past twenty years, the development of the center-fill planter has allowed producers to become more efficient by decreasing fill times. Consequently, this advancement has led to an increased concentration of weight on the center of the machine. With Mother Nature trying to shorten planting windows each year, the industry continues to look for ways to reduce the compaction issue. There are many ways to fight against compaction, such as using IF or VF tires, installing tire-pressure control systems, or converting to tracks. While helpful, these methods can be very expensive. LDM's Frame Weight Distribution (FWD) kits are one of the best solutions available.
​
​
LOW PRICE & LASTING VALUE
Most customers find that our FWD kits provide more bang for the buck than any other compaction management solution. The overall cost is very low compared to other solutions. Our kits can be installed on your existing machine and do not require trading machines, which can be extremely expensive in today’s market.
Tires and track belts will wear over time, requiring additional costs down the road when the time comes to replace them. By contrast, our FWD kits do not have high-wear components that require continuous upkeep or replacement. Additionally, the value of our FWD kits is retained through the life of the machine, resulting in increased planter value when the time comes to trade.
EASY INSTALLATION & OPERATION
Our frame weight transfer system is designed to allow for easy installation on your existing planter, either on the farm or at the dealership. Most of our customers find that a weight distribution kit is the most beneficial upgrade they have made to their machine. Once installed, the system takes care of itself, providing a carefree operation with easy adjustments. Since there are no heavy-wear components, long-term maintenance is simple and cost-free.
Although some competitors offer bolt-on style kits, our kits are designed as weld-on to ensure maximum performance and long-term durability. Competitors’ bolt-on kits rely on hardware to clamp and point-load the transferred forces to the frame. These bolt-on kits have downsized features, such as smaller cylinder bores and thinner steel plating.
Our weld-on kits allow the transferred forces to be spread out over larger areas on the frame. This results in less stress and fatigue on the planter frame and eliminates the fear of hardware coming loose over time. If you decide to invest in upgrading your planter, be sure the kit you choose provides significant results and is worth your time and money. In most cases, our weld-on kits can be installed in the same amount of time or less than our competitors’ bolt-on kits.
MULTIPLE BENEFITS
One great thing about our FWD kits is that they complement other planter solutions. Moving weight off the center of the planter not only helps reduce compaction, but also provides much-needed weight to the wings.
This is especially true with today’s higher-speed planting technology and advanced pneumatic and hydraulic row-unit downforce systems. These systems can only perform at their optimum levels if there is stability across the entire planter frame. A “wing light” planter can result in unstable row-unit ride quality, affecting planting depth and seed spacing consistency. This instability only increases for growers in no-till or reduced tillage operations which are required to use higher down pressures and have many times found themselves adding suitcase weights as their only resort.
Physics defines pressure as force divided by area. Tire, track, and inflation systems tackle the compaction problem by attempting to increase the area or footprint. FWD kits improve the issue by decreasing the force or load being applied. In other words, FWD kits remove weight from where it is unwanted and move to where it is beneficial. For this reason, we have found that many growers who have chosen other solutions also install a FWD kit to provide an added complement to their machine.
Q: HOW DOES IT WORK?
Kits use hydraulic cylinders and a control system to transfer excessive weight out to the wings. The hydraulic cylinders are positioned above the wing flex joints with the base end connecting to the center frame and the rod end connecting to the wing.
Constant flow is supplied to the control system which regulates pressure out to the cylinders. Each system is designed so that the planter still maintains its full up/down flex range of motion. The wing just sees an additional downward load that it must overcome to flex upward. The control valve is constantly monitoring the regulated side of the circuit, adding or removing oil to maintain the desired set pressure. If the planter moves over a draw and flexes down, oil is added to the regulated side to maintain the setpoint pressure. If the planter moves over a side hill and flexes up, oil is removed from the regulated side of the circuit.
​
Two types of control systems are available with all our kits:
​
​
TAILORED TO FIT YOUR MODEL
JOHN DEERE KITS
FWD kits are only available as factory options on John Deere's 60-foot DB and 1775NT machines, but LDM's retrofit kits now allow this option to be added onto all 1790, 1795, 1770NT, 1775NT, DB, and BB custom configurations. The table below provides specific information for each John Deere model. Please note, we are constantly adding new kits to our lineup, so if the model you are requesting isn’t shown below, please contact us. Likewise, many custom row and spacing configurations have been built over the years for the Deere/Bauer frames that are not listed below. Please give us a call and we can also help you with those machines.
CASE IH KITS
LDM's retrofit frame weight distribution kits now allow this option to be added onto all 1250 and 1255 configurations. The table below provides specific information for each Case IH model. Please note, we are constantly adding new kits to our lineup, so if the model you are requesting isn’t shown below, please contact us.
COMING SOON!
We are currently working on the following projects. Please contact us if you could benefit from any of these new kits:
- John Deere 1720/1725 planter kits
- John Deere 1890/1895/N500F/P500 drill kits
- John Deere 1990/N500C drill kits
- John Deere 2510 applicator kits
- Case IH 1260/1265 planter kits
- White 9812VE/9816VE/9824VE planter kits
- Kinze 3800 planter kits
​
Additionally, Wi-Fi in-cab control will soon be available for all LDM systems. This will benefit growers that may not be using an implement CAN harness on the machine. With Wi-Fi control, the system can be operated from the cab via phone or tablet.
​